In commercial juice production, you should focus on five key stages for best results. First, harvest fruits at peak maturity for quality. Next, wash and select to guarantee safety and remove contaminants. Then, use cold pressing or enzymatic methods for juice extraction to preserve flavor. After that, utilize efficient bottling techniques for consistency. Finally, prepare for high-pressure processing to enhance safety and extend shelf life. Stick around to uncover the intricacies of each phase!
Key Takeaways
- Harvesting at peak maturity ensures high-quality juice by avoiding immature or overripe fruit, which affects taste negatively.
- Washing fruits with cold running water removes dirt and pesticide residues, maintaining hygiene and nutritional integrity.
- Cold pressing and hydraulic extraction methods preserve essential nutrients and prevent oxidation, enhancing flavor and color.
- Efficient bottling techniques using food-grade bottles and automation ensure product integrity and streamline operations for large-scale production.
- High Pressure Processing (HPP) enhances juice safety, extends shelf life, and maintains freshness while meeting industrial standards.
Harvesting for Optimal Fruit Maturity
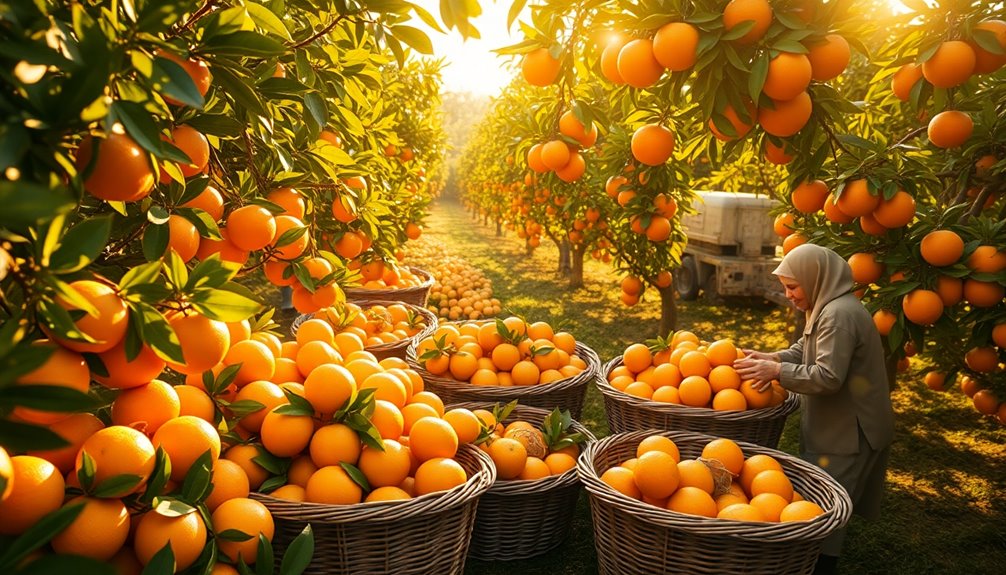
When you harvest fruits and vegetables at their peak maturity, you guarantee the highest quality juice possible. Ideal harvesting practices are vital to guarantee your raw material maintains its flavor and nutritional value.
Immature or overripe fruit can negatively affect the juice's taste, so timing is critical. Ideally, process your harvest within 24 hours to preserve vitamins and minimize food waste.
Quality assurance during harvesting involves careful selection and handling to prevent damage, which helps maintain food safety. For citrus fruits, proper ripeness prevents undesirable oils from the peel from contaminating the juice.
Washing and Selection for Safety and Quality
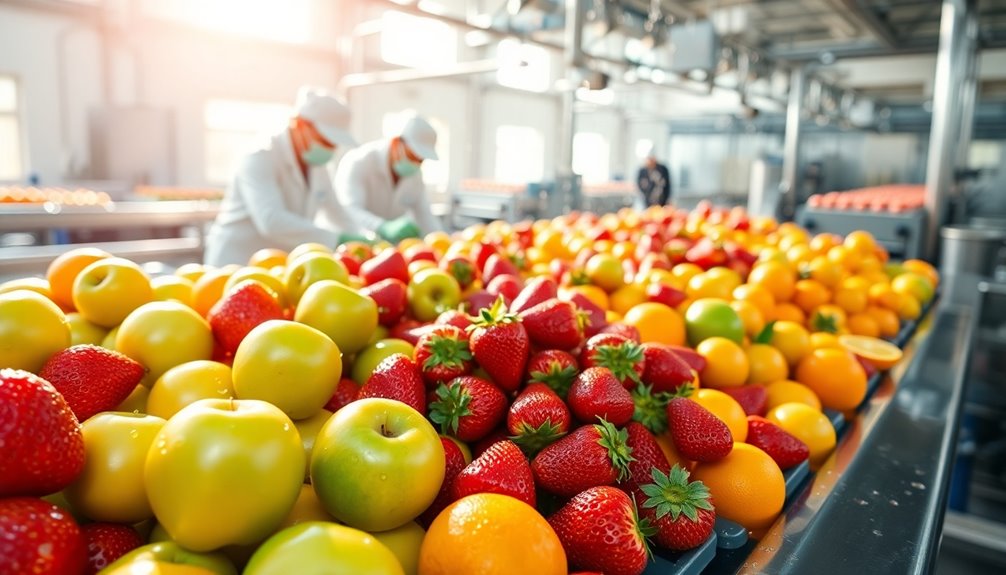
After harvesting, the next step in juice production is washing and selecting your fruits and vegetables. This process is essential for ensuring safety and quality in your fruit juices.
Washing removes dirt, dust, and pesticide residues, enhancing hygiene and prolonging shelf life. Typically, cold running water is used, which helps prevent contamination.
During the selection phase, you'll reject suboptimal fruits, guaranteeing that only high-quality ingredients make it into your juice. Proper calibration during washing can optimize juice yield, particularly in citrus fruits, while avoiding unwanted oil extraction from peels.
Effective washing and selection are important for maintaining the nutritional value and flavor integrity of your final product, ensuring that your juice stands out in the market.
Juice Extraction Methods for Flavor Preservation
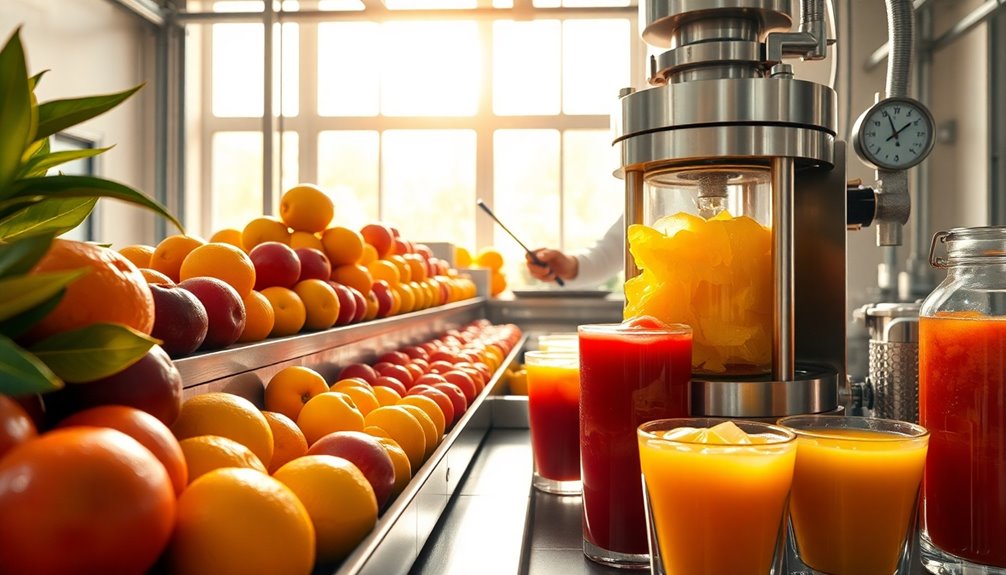
To preserve the natural flavor and nutritional value of your juice, selecting the right extraction method is essential. Here are three effective juice extraction methods for flavor preservation:
- Cold Pressing: This method crushes fruits at low temperatures, retaining essential nutrients and vibrant colors, leading to a fresher taste.
- Hydraulic Presses: By minimizing heat exposure and oxidation, hydraulic presses help maintain the juice's flavor profile while maximizing yield.
- Enzymatic Extraction: This technique breaks down cell walls to enhance juice yield without compromising flavor integrity, ensuring quality and safety in fruit processing.
Additionally, using methods like cold pressing can also help in retaining antioxidants, which are crucial for health benefits. Choosing the right juice extraction methods greatly influences your final product, allowing you to deliver a delicious and nutritious juice experience.
Efficient Bottling Techniques
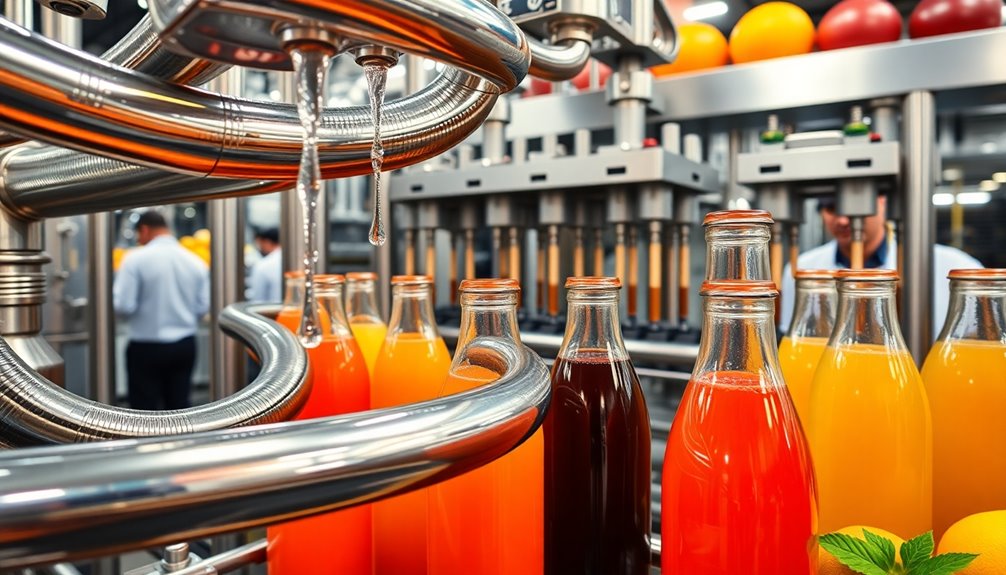
Efficient bottling techniques are essential for maximizing production while guaranteeing the quality of your juice. By utilizing industrial-scale bottling machines with up to 120 filling heads, you can achieve impressive production rates of around 1,000 units per minute. This greatly enhances your throughput and meets high quality standards.
Using food-grade bottles that don't require cleaning further secures hygiene and safety, critical in food processing. Incorporating hands-free pressure capping devices minimizes manual labor and boosts consistency in the bottling process.
Additionally, automation plays an important role in maintaining product integrity and quality while preparing for distribution. By implementing these efficient bottling techniques, you'll streamline operations and elevate your juice production to the next level.
Preparation for High Pressure Processing (HPP)
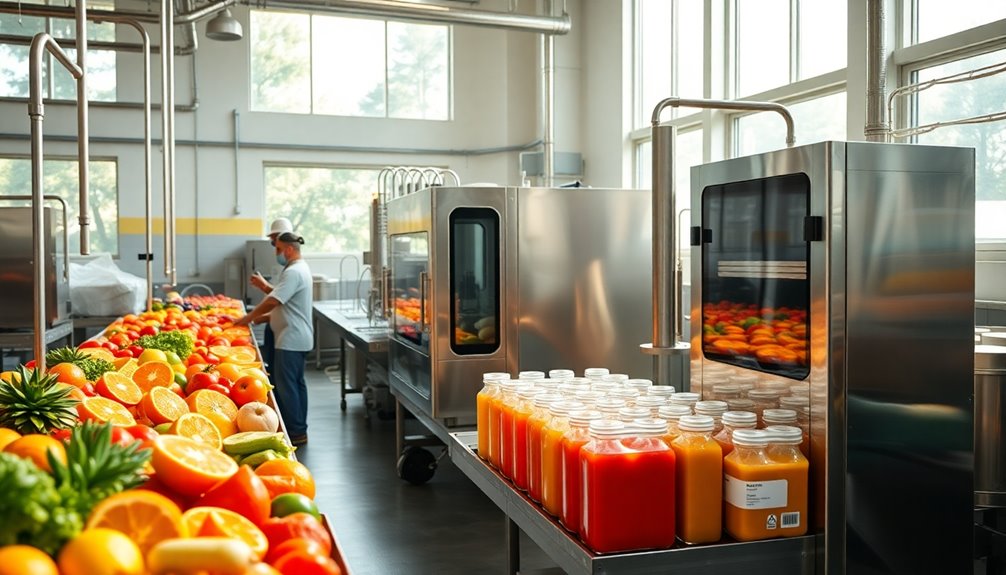
Maximizing production through efficient bottling techniques sets the stage for implementing High Pressure Processing (HPP).
This innovative method enhances juice safety and quality, ensuring you meet industrial standards while extending shelf life.
Here's how to prepare for HPP:
- Pasteurization: First, pasteurize your juice to eliminate harmful microorganisms without compromising its nutritional and organoleptic properties.
- Packaging: Use food-grade bottles designed to withstand high pressure, ensuring no cleaning is needed before filling.
- Cold Press Technique: Opt for cold press methods to maintain flavor and freshness, making your product more appealing.
Frequently Asked Questions
What Are the Steps of Juice Production?
Juice production involves several key steps.
First, you harvest fruits and vegetables at their peak for the best flavor.
Next, you wash and select the produce, removing any defects.
Then, you extract the juice using methods like mechanical or cold pressing.
After that, you pasteurize the juice to eliminate harmful microorganisms, ensuring it's safe to drink.
Finally, you bottle the juice in food-grade containers, ready for distribution to consumers.
What Are the Steps for Making Juice?
To make juice, you start by harvesting ripe fruits or vegetables.
Next, you wash them thoroughly to remove dirt and pesticides.
After that, you extract the juice using methods like pressing or centrifugal extraction, depending on the type of produce.
Once extracted, you pasteurize the juice to kill harmful microbes.
Finally, you filter and bottle the juice in food-grade containers, ensuring it's safe and ready for distribution.
Enjoy your fresh juice!
What Is the Production Process of Orange Juice?
Imagine the vibrant, sun-kissed oranges hanging from the trees, ready to be transformed into your favorite juice. You start the production process by carefully harvesting ripe oranges, ensuring they're bursting with flavor.
After a revitalizing wash, you extract the juice using specialized equipment. Next, you pasteurize it to eliminate harmful bacteria, preserving its delicious taste.
Finally, you filter and package the juice in pristine containers, ready to quench thirst and delight taste buds everywhere.
What Is the Processing at the Juice Packer?
At the juice packer, you'll first see the raw materials undergo thorough inspection to guarantee quality.
Next, the fruit is washed, extracted, and clarified, removing any impurities.
You'll notice the pasteurization process where juice is heated to kill harmful microorganisms, guaranteeing safety and extending shelf life.
Automated bottling systems then fill and seal containers rapidly, and High Pressure Processing might be used to preserve the juice's nutritional qualities without heat.
Conclusion
In commercial juice production, each phase plays an essential role in delivering a top-quality product. By focusing on harvesting ripe fruits, ensuring safety through washing and selection, preserving flavor during extraction, streamlining bottling processes, and preparing for high pressure processing, you create a juice that stands out. Remember, it’s about choosing the right ingredients, employing effective methods, and committing to quality at every stage. With these practices, you’ll not only satisfy your customers but also elevate your brand. Additionally, maintaining stringent quality control throughout the process is crucial to ensure consistency and excellence in every batch. These essential steps in juice production not only enhance the flavor profile but also contribute to the nutritional value of the final product. By prioritizing these practices, producers can cultivate a loyal customer base that appreciates the dedication to quality and taste.
Cindy thoroughly researches juicing trends, techniques, and recipes to provide readers with practical advice and inspiration. Her writing style is accessible, engaging, and designed to make complex concepts easy to understand. Cindy’s dedication to promoting the advantages of juicing shines through her work, empowering readers to make positive changes in their lives through the simple act of juicing.